

- #INKSCAPE LASER CUTTING IMPORTED IMAGE INSTALL#
- #INKSCAPE LASER CUTTING IMPORTED IMAGE SOFTWARE#
- #INKSCAPE LASER CUTTING IMPORTED IMAGE TRIAL#
We need to hit CTRL+Shift+G a couple of times to ungroup the object: Then select your file, hit OK in the following menu and move the imported structure the the top left. Just import the file by clicking File -> Import. We need to import the previously saved DXF file now. I just rarely use raster engraving anyways because it's so bloody slow and prone to ruin your part if not set up and calibrated correctly. In my template, I left out the raster engraving but it can be added easily later. So I vector engrave the coordinate origin to do that. For some reason, my laser needs kind of a heat up phase and will not cut right away otherwise. My Inkscape template adds another step 0 which ensures the laser is primed. Working in this order ensures that nothing moves out of alignment before the the part is separated from the material. Picture (raster) engravings should be done first.In additional to chaining all paths, we need to bring the work into a certain order to make sense. Unfortunately, VisiCut is not good at understanding that, so we need a way to chain all these paths before we start cutting.
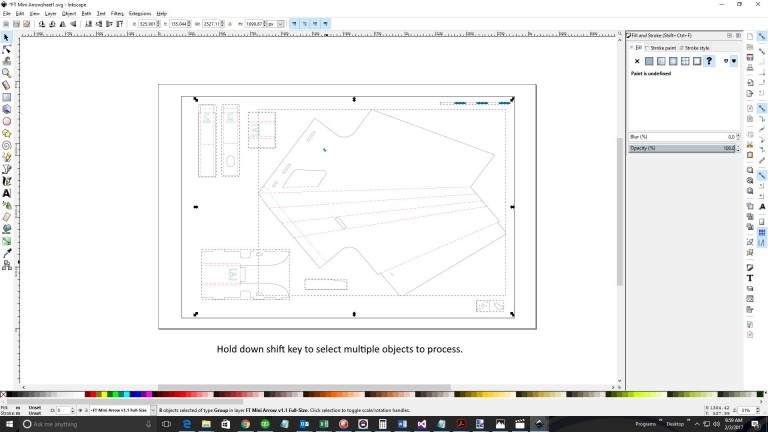
A rectangle in the exported file is represented by four individual lines that the laser happily cuts - just not in the right order which is incredibly inefficient. The dxf file that is produced by Solidworks contains individual paths. This can now be processed by Inkscape in the next step. If correctly selected sheet metal during export, these lines disappear and the cut is possible: The lines are solid and will be cut! Creating not nice living hinges and one solid part but instead three separate parts.
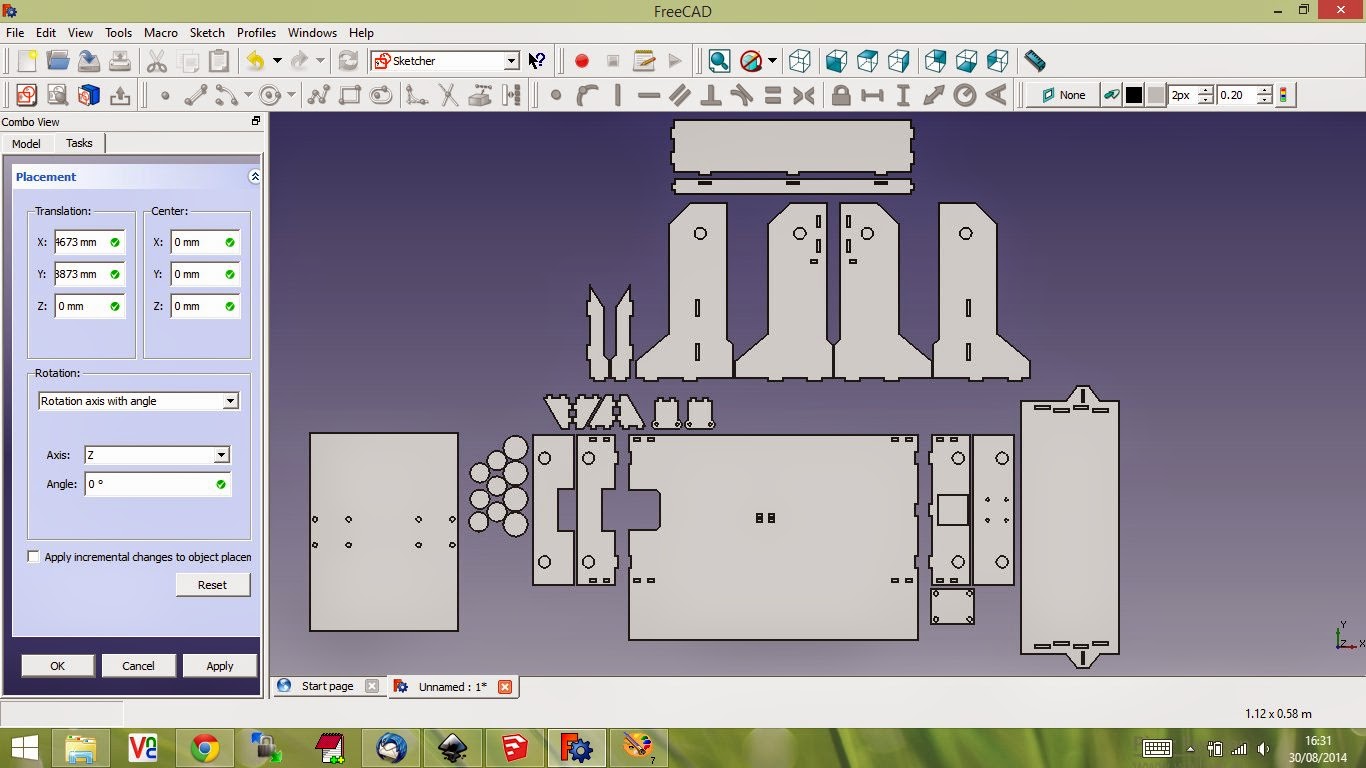
If faces / loops / edges is selected instead, those bend lines will show up in the exported DXF, ruining the part when laser cut! Look at the following example: In the image on the right, if looked at closely, you can see the bend lines on the left and right edge of the living hinges. In the menu on the left, sheet metal is selected. If you have bent sheet metal and you flatten it before exporting it, it is important to choose "sheet metal" in the following export options. Right click on the surface you want to export as a dxf file, look for Export to DXF / DWG, choose a filename and hit OK in the following menus. I never tested to make living hinges with acrylic but I guess that works as well when the material is not bent cold. Thick plywood 6mm requires larger hinges than 3mm plywood.
#INKSCAPE LASER CUTTING IMPORTED IMAGE TRIAL#
That requires a bit of trial and error as it the material properties need to be taken into account. You can easily make bent sheet metal parts on a laser but you need to design the living hinges yourself. If I need 3D parts, I use the sheet metal tools Solidworks provides. For 2D objects, laser cutting is brilliant, fast and has a very high quality. I use Solidworks for this step, most of the time. I always use the same output.nc file for the files VisiCut exports which makes this very easy to use and a 5 second process to get something to cut. With this in place, I just open a command console, enter SimpleG.bat and the process starts. You obviously need to adjust all paths to your filesystem and the comport to the comport your GRBL communicates through, but you get the idea. Where ever you are at this moment, I recommend creating a batch file and add this command: "G:\Seafile\Software\CNC Software\Laser Cutter\SimpleG\bin\ release\SimpleG.exe " -p COM5 -f "e:\ Users\timob\Documents\output.nc " -F "G:\Seafile\Software\CNC Software\Laser Cutter\SimpleG\ bin\ release\SimpleG-end.gcode " Open a console (hit Win, enter "cmd", hit enter).
#INKSCAPE LASER CUTTING IMPORTED IMAGE INSTALL#
Install and download everything in the above order.
#INKSCAPE LASER CUTTING IMPORTED IMAGE SOFTWARE#
